Explore the world of IPSE, the Integrated Process Simulation Environment, designed for precise heat and mass balance calculations and advanced process simulations. Learn how this powerful tool is transforming industries like thermal power, solar power, refrigeration, and desalination with its flexible, modular design and comprehensive capabilities.
What is IPSE?
IPSE, short for Integrated Process Simulation Environment, is the foundation for our leading software solution for heat and mass balance calculation and process simulation. The software is primarily used for simulating and optimizing thermodynamic cycles in power plants. Developed through numerous iterations and designed with modular flexibility, the IPSE product family stands out as an efficient tool capable of addressing complex tasks across diverse domains, including thermal power, solar power, refrigeration, desalination, ORC and low temperature power.
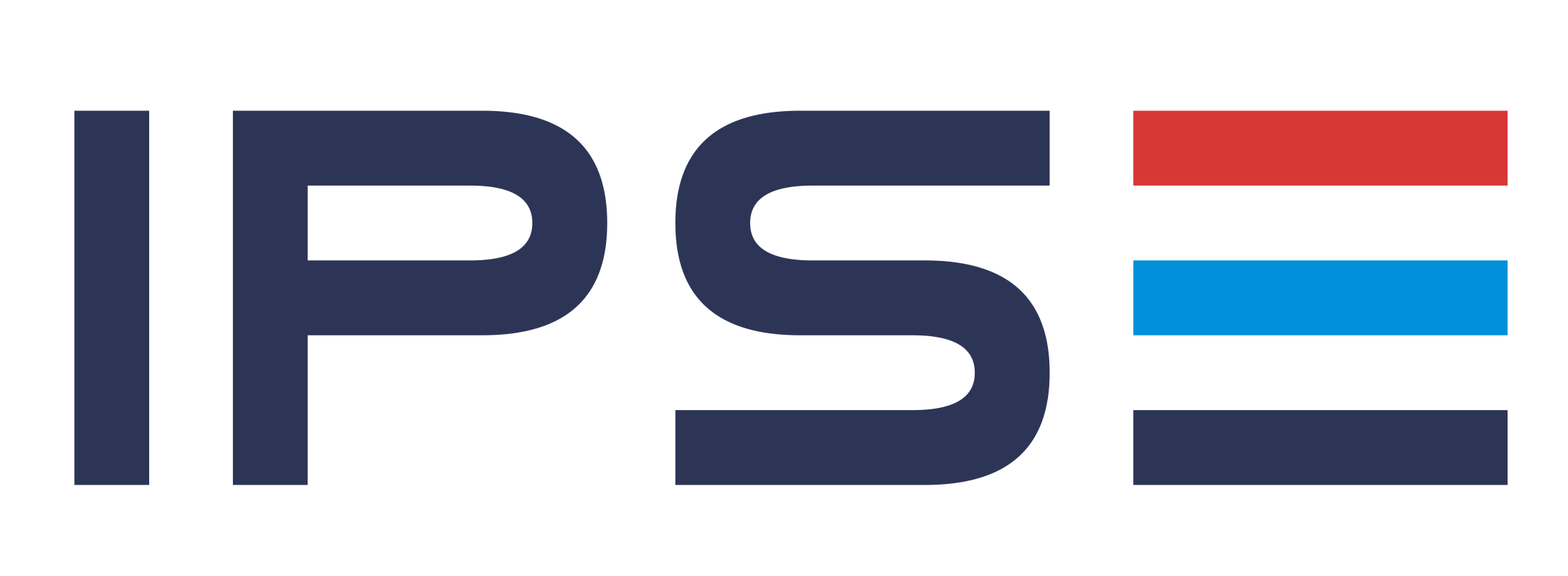
What is Process Simulation for Heat and Mass Balancing?
Process simulation for heat and mass balancing is a vital technique in chemical engineering and allied disciplines, aimed at optimizing and analyzing industrial processes. This approach employs advanced software to craft detailed models that mimic real-world systems under diverse conditions. By simulating the movement of materials and energy within a process, engineers can precisely predict the effects of changes in operational parameters on efficiency, safety, and output. This foresight enables the detection of potential bottlenecks, inefficiencies, and safety risks before they manifest in the actual process.
Moreover, it supports the design of new processes and the enhancement of existing ones to meet performance targets, ensuring both cost-effectiveness and sustainability. Integrating heat and mass balancing in process simulation is crucial for optimizing thermal and material use, minimizing waste, and boosting overall system performance.
Key Features of IPSE
One of IPSE’s key strengths lies in its extensive libraries and models. These libraries are equipped with predefined models and components tailored to various industries, covering power plant design, thermal modeling, chemical process simulation, and energy optimization. The availability of these comprehensive resources enables users to quickly set up simulations, allowing them to focus on detailed analysis rather than on the preliminary configuration of the models.
Furthermore, IPSE supports a wide range of simulation types, including both steady-state and dynamic simulations. This flexibility is crucial for accurately modeling processes under different operating conditions. Whether users are working on power steam cycles, combined cycle cogeneration systems, or gas turbine cogeneration systems, IPSE facilitates detailed thermodynamic optimization, energy system modeling, and mass transfer calculations. This ensures that the processes are simulated efficiently and effectively, catering to diverse industrial requirements.
Despite its advanced capabilities, IPSE features a user-friendly interface designed to simplify the complex process of simulation. The platform includes drag-and-drop functionality, customizable dashboards, and straightforward navigation, making it easy for users to build and modify models, visualize data, and interpret results. This intuitive design makes IPSE accessible to engineers and researchers across various disciplines, from industrial engineering to process modeling, thus broadening its applicability and user base.
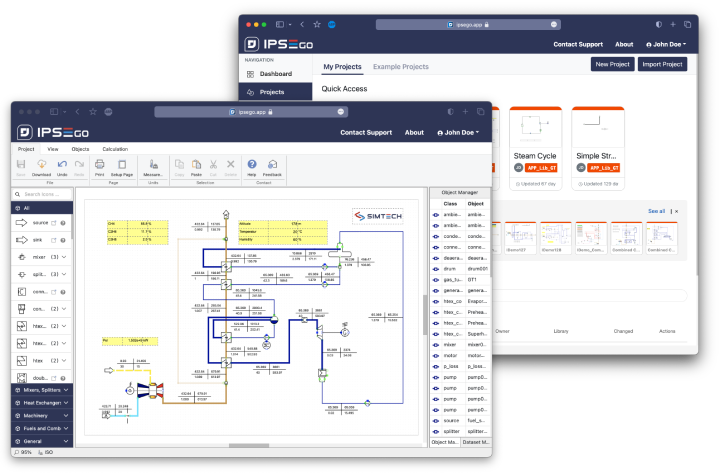
Example Applications of IPSE
IPSE is extensively used in power generation to enhance the efficiency and performance of power cycles. It supports diverse configurations, including steam power plants and gas turbines, allowing engineers to simulate different operating conditions. This capability enables users to optimize the power generation process, leading to improved system performance and energy efficiency. By accurately modeling these processes, IPSE helps in identifying potential improvements and innovations in power generation technologies.
In the chemical industry, IPSE serves as a vital tool for the design and optimization of various processes. It aids in the development of reactors, separation processes, and heat exchangers by providing detailed chemical simulation and modeling capabilities. Chemical engineers and researchers rely on IPSE to simulate complex chemical reactions and separation mechanisms, which facilitates the design of more efficient and cost-effective chemical processes. The ability to predict the behavior of chemical systems under different conditions makes IPSE an indispensable resource in chemical processing.
Environmental engineers utilize IPSE to model and optimize processes related to waste treatment, emissions control, and resource recovery. Its advanced energy simulation and process simulation tools are crucial for assessing the environmental impact of industrial activities. By simulating waste treatment processes and emissions scenarios, IPSE helps engineers develop strategies to minimize environmental pollution and enhance resource efficiency. This application is vital for creating sustainable engineering solutions and ensuring regulatory compliance in environmental management.
These are some example industries and applications for the Integrated Process Simulation Environment. Its ability to model complex systems and optimize processes supports engineers and researchers in improving efficiency, reducing costs, and minimizing environmental impact across these industries.
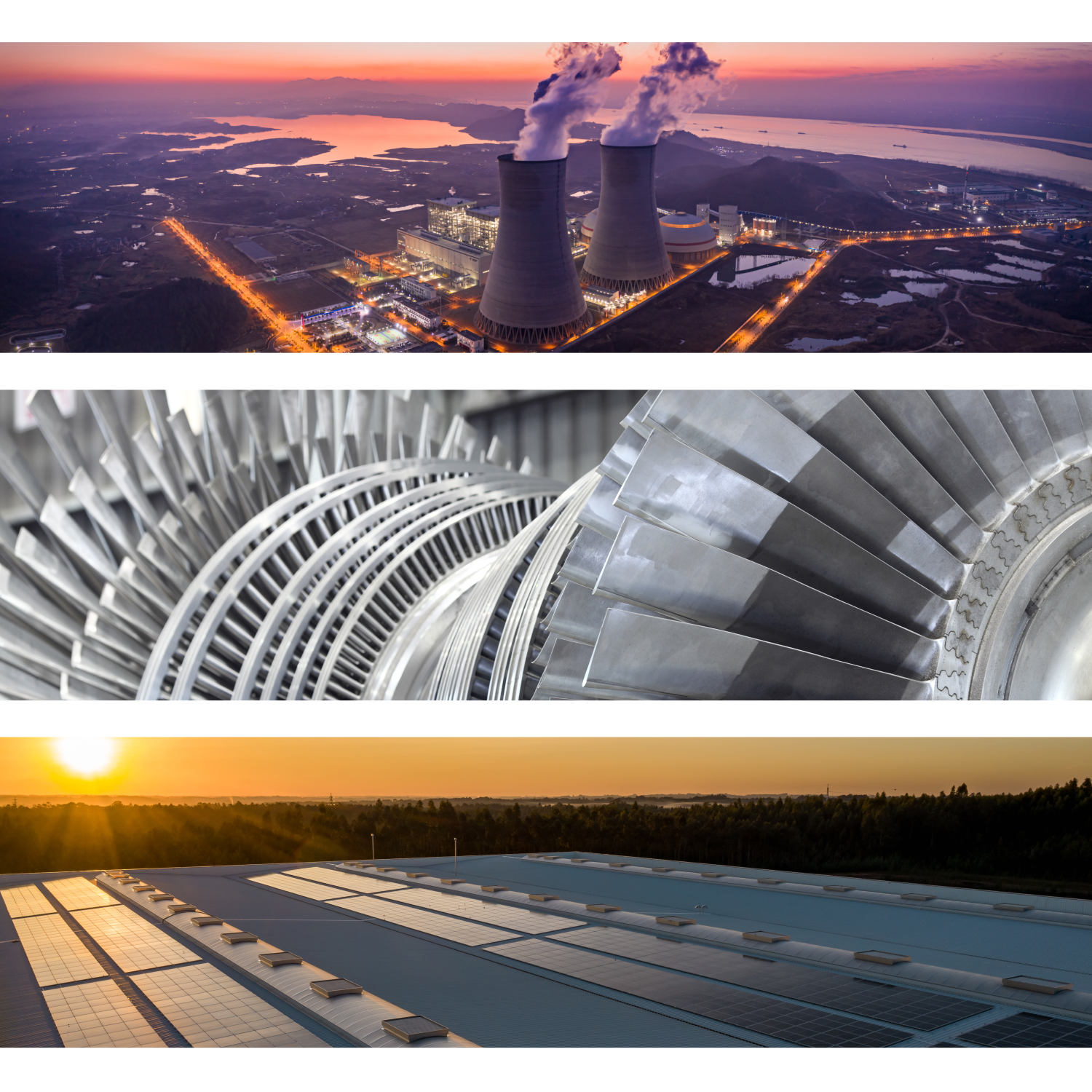
Understanding the Goal for Your Simulation Needs
When approaching process simulation, it’s critical to have a clear understanding of your objectives. Are you aiming to optimize efficiency, reduce emissions, improve safety, or enhance productivity? Defining these goals at the outset helps in selecting the right simulation parameters and focus areas, ensuring that the simulation provides meaningful and actionable insights. IPSE's comprehensive capabilities allow users to align their simulations with specific objectives, facilitating targeted improvements and innovations.
Which Issues Can Impact Your Simulation Progress?
Several factors can impact the progress and success of your simulations. Data accuracy is paramount; using incorrect or incomplete data can lead to flawed models and unreliable results. Additionally, computational resources and software limitations may pose challenges, particularly for complex simulations requiring high levels of detail and precision. User expertise is also a significant factor – even the most advanced tools require knowledgeable operators to set up and interpret simulations effectively. IPSE addresses these issues by offering robust data integration, high-performance computing capabilities, and a user-friendly interface that simplifies the simulation process.
Using Simulation Results for Real-world Applications
The true value of process simulation lies in its application to real-world scenarios. Once simulations are complete, the results can inform decision-making, optimize operations, and guide the implementation of new technologies or processes. For example, in power generation, simulation results can lead to adjustments in operational parameters to enhance efficiency. They can inform the design of more effective reactors or separation units in chemical processing. By translating simulation insights into practical actions, engineers can significantly improve performance, cost savings, and environmental sustainability. IPSE's detailed and accurate simulations provide a solid foundation for making these critical decisions.
IPSE Products
Learn more about the differences between our two IPSE products: IPSEpro and IPSE GO